First of all, what is GRN and why is it important?
A goods receipt note (GRN) is created to serve as a direct record confirming goods have been delivered corresponding to a purchase. A GRN is a critical document for not just the Accounts Payable department, but for warehouse personnel, procurement officials, and even the entire supply chain department as well.
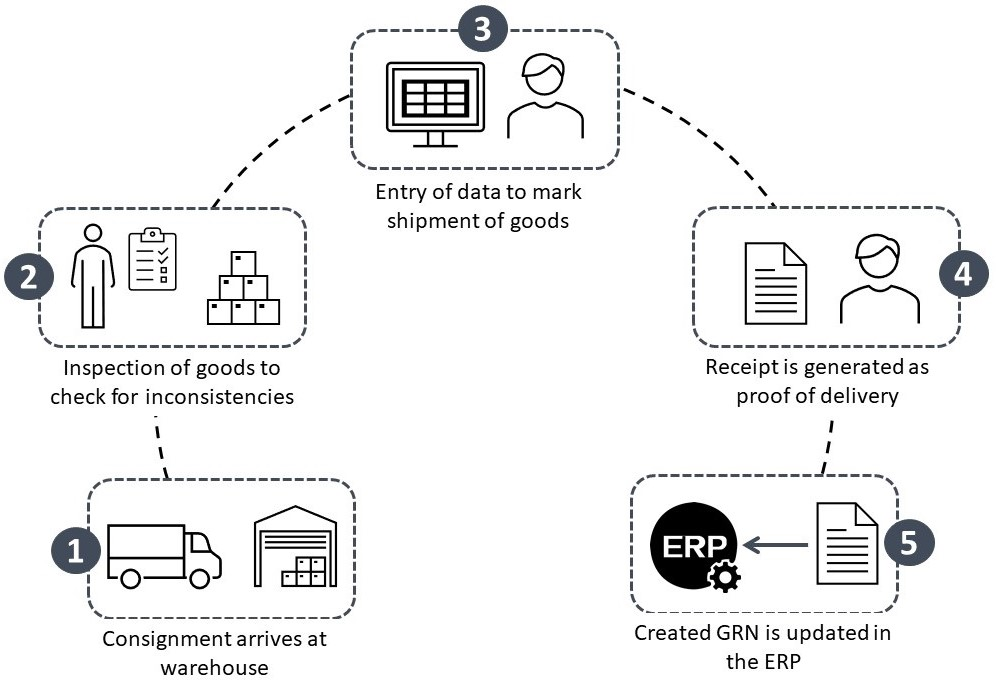
Figure 1:Steps involved in a typical GRN process
A GRN directly corresponds to both goods that have been ordered and those received upon delivery. Therefore, it acts as an acknowledged reference document for the buyer to match and compare it with purchase orders and invoices for payment processing as per the terms agreed.
The problem with a manual GRN creation process
Typically, when a shipment arrives at a warehouse, there is a series of processes that follows: Consignments wait at the gate to be marked for clearance, followed by a manual inspection of goods, GRN creation for goods received, and, finally, ERP updates.
As essential as it may be, GRN creation can also lead to a long and tedious process for the employees involved – especially if the shipment of goods being received is frequent/regular.
Needless to say, this increases the waiting period tremendously for both the buyer and the transporter. It also impedes assembly line activities due to slow inventory updates, not to mention the paperwork involved in clearing all field activities.
Eventually, delays in GRN creation can also heavily impact invoice processing, approvals, payments. For shipments to be approved, the GRN must be matched against the purchase order and the order received to ensure the payment is only made upon the fulfillment of previously agreed-upon terms. With manual processes, exceptions like data mismatch, document misplacement, and mis-shipment of goods can lead to unwanted bottlenecks, thereby inhibiting productivity.
In fact, according to a study, such invoice and payment processing exceptions are the biggest obstacle for AP as per 62% of the surveyors. Out of those exceptions, discrepancies between POs, invoices, and GRNs seemed to be the root problem, as 82% of the respondents claim this to be the top source of exceptions.
What comes next?
Digitization has forced businesses to a point where manual processes fail to even be considered a competent alternative. The supply chain remains as a dominant factor that encapsulates all primary processes involved in a business transaction. Now, the importance of streamlining not only concerns successful, on-time deliveries, but optimizing each step of the process as well to ensure overall productivity.
This is where GRN automation can play a vital role. Eliminating manual dependencies can increase efficiency, reduce error, and help accelerate the entire procurement cycle.
Read our blog on GRN automation to learn more